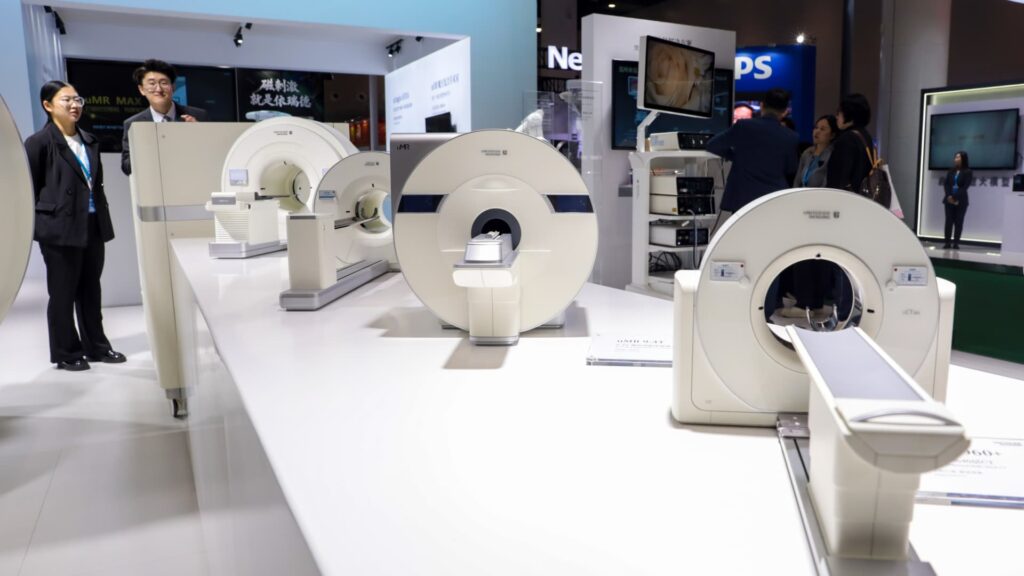
Medical Industry Tariff Divide: Manufacturers Split on Trump's Trade Policies
Medical Industry Tariff Divide: Manufacturers Split on Trump’s Trade Policies
Published on April 20, 2025
Medical equipment manufacturers are facing a complex landscape as Trump’s tariff policies create a divide between device makers and PPE producers. (Image: Representative)
Table of Contents
President Donald Trump’s aggressive tariff policies have created a significant medical industry tariff divide, with manufacturers taking opposing positions based on how the import duties affect their business models. While medical device makers seek exemptions to avoid disruptions and cost increases, domestic personal protective equipment (PPE) producers are embracing the tariffs as a competitive advantage against foreign imports. This split highlights the complex economic implications of trade policy on healthcare costs, patient care, and domestic manufacturing priorities.
The Medical Industry Tariff Divide
The medical industry tariff divide has emerged as a notable consequence of the Trump administration’s latest round of import duties. Unlike during Trump’s first term, when medical devices and protective gear from China, Mexico, and Canada received exemptions from tariffs, the current policy offers no such carve-outs. This policy shift has created two distinct camps within the healthcare manufacturing sector.
The stark divide in the medical manufacturing industry reflects broader tensions in U.S. trade policy. Medical device manufacturers that rely on global supply chains and international component sourcing face significant cost increases, while domestic PPE producers see an opportunity to reclaim market share lost to subsidized foreign competitors. This division mirrors similar conflicts in other industries where the benefits and costs of protectionist policies are unevenly distributed.
Device Makers Push for Exemptions
Medical technology and device manufacturers are at the forefront of opposition to the tariffs, with industry groups like AdvaMed actively lobbying for exemptions. These companies argue that the medical industry tariff divide threatens to increase healthcare costs, disrupt supply chains, and potentially compromise patient care by limiting access to critical equipment.
Companies like Aeroflow Health, which provides insurance-covered medical devices ranging from breast pumps to CPAP machines for sleep apnea patients, have been actively lobbying Congress for either an overall MedTech tariff exemption or a longer implementation timeline. These businesses find themselves in a particularly challenging position because their contracts with insurers often lock in prices for the year, making it difficult to pass on increased costs.
The medical device industry’s concerns highlight a key aspect of the medical industry tariff divide: the inability to simply pass costs through to consumers due to the regulated nature of healthcare pricing and insurance contracts. This structural limitation makes the sector particularly vulnerable to sudden cost increases from tariff policies.
PPE Manufacturers Welcome Tariffs
On the opposite side of the medical industry tariff divide, domestic manufacturers of personal protective equipment have enthusiastically welcomed the new tariffs. These companies, which struggled to compete with lower-priced imports from China even during the heightened demand of the COVID-19 pandemic, see the tariffs as creating a more level playing field.

A U.S.-based PPE manufacturing facility. Domestic producers support tariffs as a way to compete with lower-priced Chinese imports. (Image: Representative)
American PPE manufacturers point to what they consider unfair competition from Chinese producers, who benefit from government subsidies and lower operating costs. Analysts at Boston Consulting Group estimate that approximately half of the PPE used in the United States is produced in China, with an additional 10%-15% coming from Canada and Mexico.
For companies like Altor Safety, which manufactures masks, N95 respirators, and gloves in the United States, the tariffs could be transformative. Despite securing contracts with the U.S. government and major corporations like FedEx, Altor has struggled to gain market share with healthcare systems due to price competition from Chinese manufacturers. The company’s president, Thomas Allen, expressed optimism that the tariffs could help win new contracts, noting that as production volumes increase, “we can actually lower our prices.”
Hospital and Patient Cost Implications
Healthcare providers find themselves caught in the middle of the medical industry tariff divide, facing potential cost increases and supply chain uncertainties that could affect patient care. Major hospital organizations have joined device manufacturers in expressing concern about the tariffs’ implications.
The concern extends beyond immediate cost increases to potential long-term impacts on healthcare accessibility and quality. If tariffs remain in place, they could eventually contribute to higher insurance premiums, increased out-of-pocket costs for patients, and greater financial strain on already-pressured healthcare systems.
Potential Healthcare Impacts of Tariff Policies
- Higher Equipment Costs: Immediate price increases for imported medical devices and components
- Taxpayer Burden: Increased costs for Medicare, Medicaid, and VA healthcare programs
- Supply Chain Disruptions: Potential shortages or delays in critical medical equipment
- Hospital Financial Strain: Fixed reimbursement rates with higher equipment costs squeeze margins
- Patient Care Implications: Possible reduced access to certain treatments or technologies
- Insurance Premium Increases: Long-term pass-through of higher costs to health insurance rates
This impact on healthcare providers and patients represents one of the most significant concerns in the medical industry tariff divide, as it extends the consequences beyond the manufacturing sector to the broader healthcare ecosystem and ultimately to patient outcomes.
Supply Chain Challenges and Adaptations
The medical industry tariff divide is forcing manufacturers to reconsider their supply chain strategies, with many looking for ways to mitigate the impact of the new duties. While the Trump administration has promoted tariffs as a way to encourage domestic manufacturing, industry experts suggest that in the near term, many companies are more likely to shift production to other countries with lower tariff rates rather than relocating to the United States.
Supply Chain Challenges
- Complex international component sourcing networks difficult to quickly restructure
- Specialized manufacturing capabilities not readily available in all locations
- Regulatory approvals required for production facility changes
- Higher costs for U.S. manufacturing compared to many alternative locations
- Uncertainty about duration of tariff policies complicates long-term planning
Adaptation Strategies
- Production shifting to Mexico and Canada to leverage potential USMCA exemptions
- Diversification of manufacturing locations to reduce dependency on any single country
- Supply chain redesign to source components from non-tariffed regions
- Increased inventory levels to buffer against supply disruptions
- Exploration of alternative materials and components to reduce tariff exposure
These supply chain challenges highlight another dimension of the medical industry tariff divide: the practical difficulties of rapidly transforming global manufacturing networks. As Vikram Aggarwal, a Boston Consulting Group managing director and partner, noted: “Managing that and the complexity there becomes super hard.”
Many major medical technology and device manufacturers already maintain production facilities across multiple countries, which provides some flexibility in navigating tariff challenges. Analysts at Canaccord Genuity note that companies like Zimmer Biomet and Stryker, two of the largest makers of knee replacements, have dozens of facilities across North America, Europe, and Asia that help them manage tariff impacts, though they will still face financial consequences from the new duties.
Johnson & Johnson’s $400M Tariff Impact
The scale of the financial impact from the medical industry tariff divide is illustrated by Johnson & Johnson’s recent disclosures. The healthcare giant has calculated that its MedTech division, which produces orthopedic and cardiac implants, could face a $400 million tariff-related cost increase this year. This substantial amount stems primarily from the high duties on Chinese imports and levies on non-USMCA compliant imports from Canada and Mexico.

Johnson & Johnson medical devices. The company expects a $400 million tariff impact on its MedTech division this year. (Image: Representative)
As one of the first major medical technology firms to report first-quarter results, J&J’s comments provide valuable insight into how the sector is grappling with the new trade environment. CFO Joseph Wolk explained during the company’s earnings call that existing contracts with hospitals make it difficult to raise prices in the near term, creating significant margin pressure.
J&J’s $400M Tariff Impact Breakdown
- Chinese Import Duties: 145% tariffs on components and finished products
- USMCA Non-Compliance: Additional costs for Canadian and Mexican imports
- Fixed-Price Contracts: Limited ability to pass costs to healthcare customers
- Global Supply Chain: Complex network difficult to quickly reconfigure
- Long Product Development Cycles: Difficult to quickly redesign for different manufacturing locations
Johnson & Johnson’s experience exemplifies the challenges faced by companies on one side of the medical industry tariff divide. As a global manufacturer with extensive operations and diverse product lines, the company has more flexibility than smaller manufacturers but still faces substantial financial impacts from the new tariff regime.
Manufacturing Incentives: Tariffs vs. Tax Policy
The medical industry tariff divide has sparked debate about the most effective policy approaches to encourage domestic medical manufacturing. While the Trump administration has emphasized tariffs as a key tool to promote U.S. production, some industry leaders suggest that tax incentives might provide more effective and less disruptive motivation for domestic investment.
J&J’s CEO highlighted that the company is already investing $55 billion over four years to produce advanced medications in America, driven in part by existing tax incentives. This perspective suggests that the medical industry tariff divide might be bridged through alternative policy approaches that achieve similar domestic manufacturing goals without the same supply chain disruptions and healthcare cost impacts.
Comparing Manufacturing Incentive Approaches
Policy Feature | Tariff Approach | Tax Incentive Approach |
---|---|---|
Implementation Speed | Fast to implement | Usually requires legislative process |
Market Disruption | Significant immediate disruption | Lower immediate market impact |
Healthcare Cost Impact | Can increase costs immediately | Less direct impact on healthcare costs |
Long-term Planning | Creates uncertainty for investment | Provides stable framework for decisions |
New Facility Investment | Mixed incentive effect | Direct incentives for new facilities |
Supply Chain Transition | Forces rapid, potentially disruptive changes | Allows for planned, gradual transitions |
This debate over policy approaches represents a potential path toward resolving the medical industry tariff divide. While the current situation has created clear winners and losers within the industry, alternative policies might achieve similar domestic manufacturing goals while distributing benefits and costs more evenly across the sector.
As the healthcare industry continues to navigate this challenging trade environment, the tension between protecting domestic manufacturing and ensuring affordable, accessible medical care remains at the heart of the medical industry tariff divide. How policymakers address this tension will have significant implications for healthcare costs, patient care, and the future of medical manufacturing in the United States.
Published on April 20, 2025 | Updated on April 20, 2025